Automation in Perfume Filling Packaging: Enhancing Efficiency and Quality
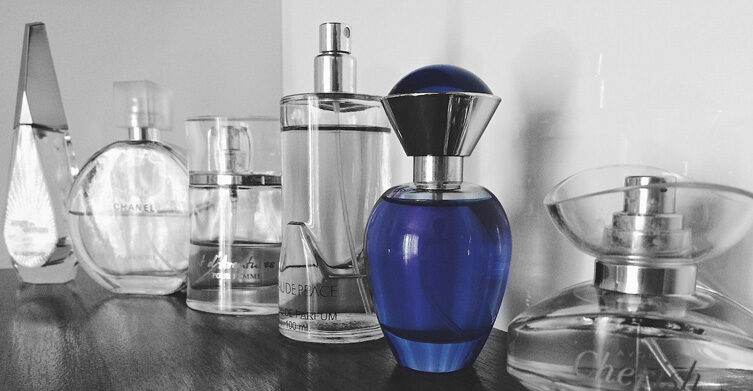
In the world of perfume production, the importance of efficient and high-quality packaging cannot be overstated. Perfume filling packaging machines have revolutionized the industry, allowing manufacturers to streamline their processes and meet the demands of the market. Among the various advancements in this field, automation stands out as a game-changer. Automation technology has transformed perfume filling and packaging, offering unparalleled benefits in terms of efficiency, accuracy, and overall product quality. This article explores the impact of automation in perfume filling packaging, highlighting its numerous advantages and discussing how it has raised the bar for the industry.
Streamlined Filling Process:
Automation has significantly improved the filling process of perfume packaging. With the integration of utomated filling machines, the task of filling perfume bottles is executed swiftly and accurately. These machines are designed to handle a wide range of bottle sizes and shapes, providing flexibility and adaptability to meet the diverse needs of manufacturers. The precise control and consistency of the automated filling process minimize wastage and ensure that every bottle is filled to the exact desired level, eliminating variations in product quantity and quality.
Increased Efficiency and Productivity:
Automated perfume filling packaging machines offer unparalleled efficiency and productivity gains. They can handle high-speed production lines, accommodating large volumes of perfume bottles in a shorter time frame. The speed and accuracy of these machines optimize the production process, reducing downtime and maximizing output. This increased efficiency translates into significant cost savings and improved competitiveness for perfume manufacturers.
Automation technology has revolutionized quality control in perfume filling packaging. These machines are equipped with advanced sensors and computer vision systems that ensure precise measurement and detection of any irregularities during the filling and packaging process. Automated quality control mechanisms can detect variations in liquid levels, faulty caps, and even label positioning, allowing for immediate corrective action. This level of accuracy and control guarantees that each perfume bottle meets the highest standards of quality before it reaches the consumer.
Reduction in Human Error:
Human error is a common challenge in manual filling and packaging processes. Automation minimizes the risk of human error, leading to improved product quality and consistency. By automating repetitive tasks, such as bottle positioning, filling, and capping, the potential for mistakes is greatly reduced. Additionally, automated machines are less prone to fatigue, ensuring a higher level of accuracy throughout the production process.
Improved Safety and Hygiene:
Automation in perfume filling packaging promotes enhanced safety and hygiene standards. Perfume filling machines are designed to meet strict regulatory requirements, ensuring that the packaging process adheres to health and safety guidelines. Automated systems minimize the risk of contamination, as they operate in a controlled environment with minimal human contact. Moreover, these machines are equipped with features such as automatic cleaning and sterilization, further enhancing the overall cleanliness and safety of the process.
Automation has transformed the landscape of perfume filling packaging, revolutionizing the industry with its efficiency, accuracy, and quality control capabilities. Through streamlined filling processes, increased efficiency, enhanced accuracy, and improved safety standards, automated perfume filling packaging machines have become indispensable tools for manufacturers. As the demand for high-quality perfume products continues to rise, embracing automation technology has become crucial for companies striving to stay competitive and deliver exceptional products to consumers. The future of perfume packaging lies in automation, as it offers unrivaled advantages that are transforming the industry one bottle at a time.